Some Known Incorrect Statements About Alcast Company
Table of ContentsAll About Alcast CompanyFascination About Alcast CompanyHow Alcast Company can Save You Time, Stress, and Money.The Basic Principles Of Alcast Company Some Ideas on Alcast Company You Need To KnowAn Unbiased View of Alcast Company
The subtle difference hinges on the chemical web content. Chemical Comparison of Cast Aluminum Alloys Silicon promotes castability by lowering the alloy's melting temperature level and enhancing fluidness throughout spreading. It plays a critical function in enabling complex molds to be filled accurately. Additionally, silicon contributes to the alloy's stamina and put on resistance, making it important in applications where sturdiness is critical, such as automobile parts and engine components.It additionally improves the machinability of the alloy, making it much easier to process right into ended up products. In this way, iron adds to the overall workability of light weight aluminum alloys. Copper increases electric conductivity, making it beneficial in electrical applications. It additionally enhances rust resistance and includes to the alloy's general stamina.
Manganese adds to the strength of light weight aluminum alloys and enhances workability (aluminum casting company). It is typically utilized in functioned light weight aluminum products like sheets, extrusions, and accounts. The existence of manganese help in the alloy's formability and resistance to cracking during construction processes. Magnesium is a lightweight element that provides strength and effect resistance to aluminum alloys.
The Of Alcast Company
It allows the production of light-weight parts with superb mechanical residential properties. Zinc enhances the castability of light weight aluminum alloys and aids manage the solidification procedure during spreading. It boosts the alloy's strength and solidity. It is commonly found in applications where elaborate shapes and fine details are needed, such as ornamental spreadings and certain vehicle components.
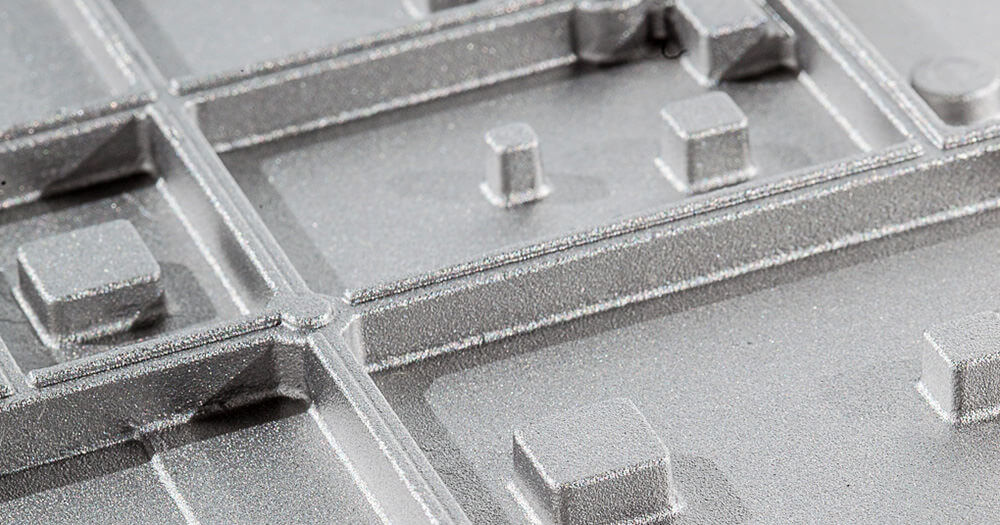
The main thermal conductivity, tensile stamina, yield strength, and elongation vary. Select appropriate basic materials according to the performance of the target item generated. Among the above alloys, A356 has the highest thermal conductivity, and A380 and ADC12 have the lowest. The tensile limit is the contrary. A360 has the best yield stamina and the highest possible prolongation rate.
The Alcast Company PDFs
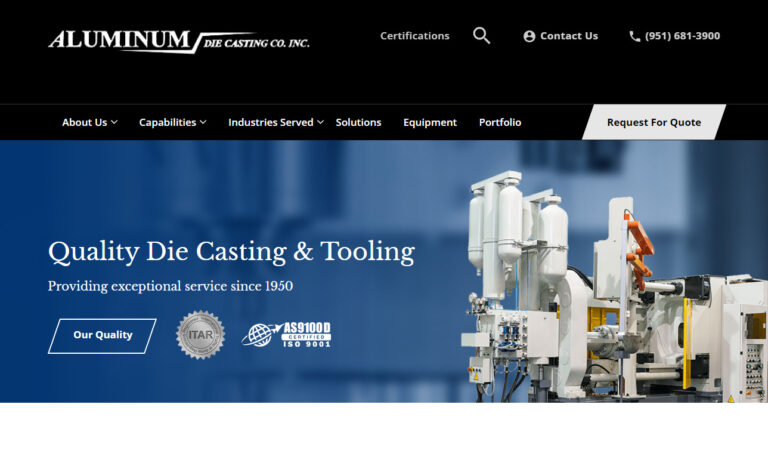
In precision spreading, 6063 is fit for applications where intricate geometries and high-grade surface coatings are vital. Examples consist of telecommunication enclosures, where the alloy's superior formability enables smooth and visually pleasing styles while keeping structural honesty. Likewise, in the Lighting Solutions industry, precision-cast 6063 components create stylish and effective lights fixtures that call for elaborate shapes and great thermal performance.
It leads to a better surface area coating and much better corrosion resistance in A360. In addition, the A360 shows exceptional prolongation, making it optimal for complex and thin-walled elements. In precision spreading applications, A360 is well-suited for sectors such as Consumer Electronic Devices, Telecommunication, and Power Devices. Its enhanced fluidness permits complex, high-precision parts like smart device casings and communication tool housings.
The 5-Second Trick For Alcast Company
Its unique homes make A360 an important option for accuracy spreading in these sectors, enhancing product longevity and high quality. Light weight aluminum alloy 380, or A380, is a widely utilized spreading alloy with a number of unique characteristics. It provides outstanding castability, making it a perfect selection for accuracy casting. A380 exhibits good fluidity when molten, guaranteeing intricate and comprehensive molds are accurately replicated.
In accuracy casting, aluminum 413 shines in the Consumer Electronic Devices and Power Equipment sectors. This alloy's superior rust resistance makes it an excellent selection for exterior applications, making sure durable, sturdy products in the pointed out sectors.
Some Known Questions About Alcast Company.
When you have decided that the light weight aluminum die casting process is suitable for your task, an essential following step is picking the most suitable alloy. The aluminum alloy you choose will considerably impact both the casting procedure and the buildings of the end product. Since of this, you need to make your decision thoroughly and take an enlightened strategy.
Identifying the most suitable aluminum alloy for your application will mean evaluating a broad selection of qualities. These relative alloy characteristics adhere to the North American Die Casting Organization's standards, and we have actually split them right into two categories. The very first group addresses alloy qualities that influence the production procedure. The second covers features influencing the buildings of the last product.
7 Simple Techniques For Alcast Company
The alloy you choose for die spreading straight impacts a number of aspects of the spreading process, like exactly how very easy the alloy is to collaborate with and if it is vulnerable to casting issues. Warm fracturing, likewise recognized as solidification fracturing, is a typical die spreading flaw for light weight aluminum alloys that can result in inner or surface-level rips or splits.
Particular light weight aluminum alloys are more at risk to hot breaking than others, and your choice must consider this. It can harm both the cast and the die, so you should look for alloys with high anti-soldering homes.
Deterioration resistance, which is currently a notable characteristic of aluminum, can vary significantly from alloy to alloy and is a crucial characteristic to consider relying on the environmental conditions your item will be subjected to (Foundry). Wear resistance is an additional home commonly sought in aluminum products and can separate some alloys